大手照明機器メーカーB社様
B社の物流体制は倉庫管理が煩雑で、在庫分散や過剰生産、輸送効率が低下し物流コスト増加を招いている
ポイント
- マザーセンターを設置
- マザーセンターから顧客へ直接配送の実施
課題・お悩み
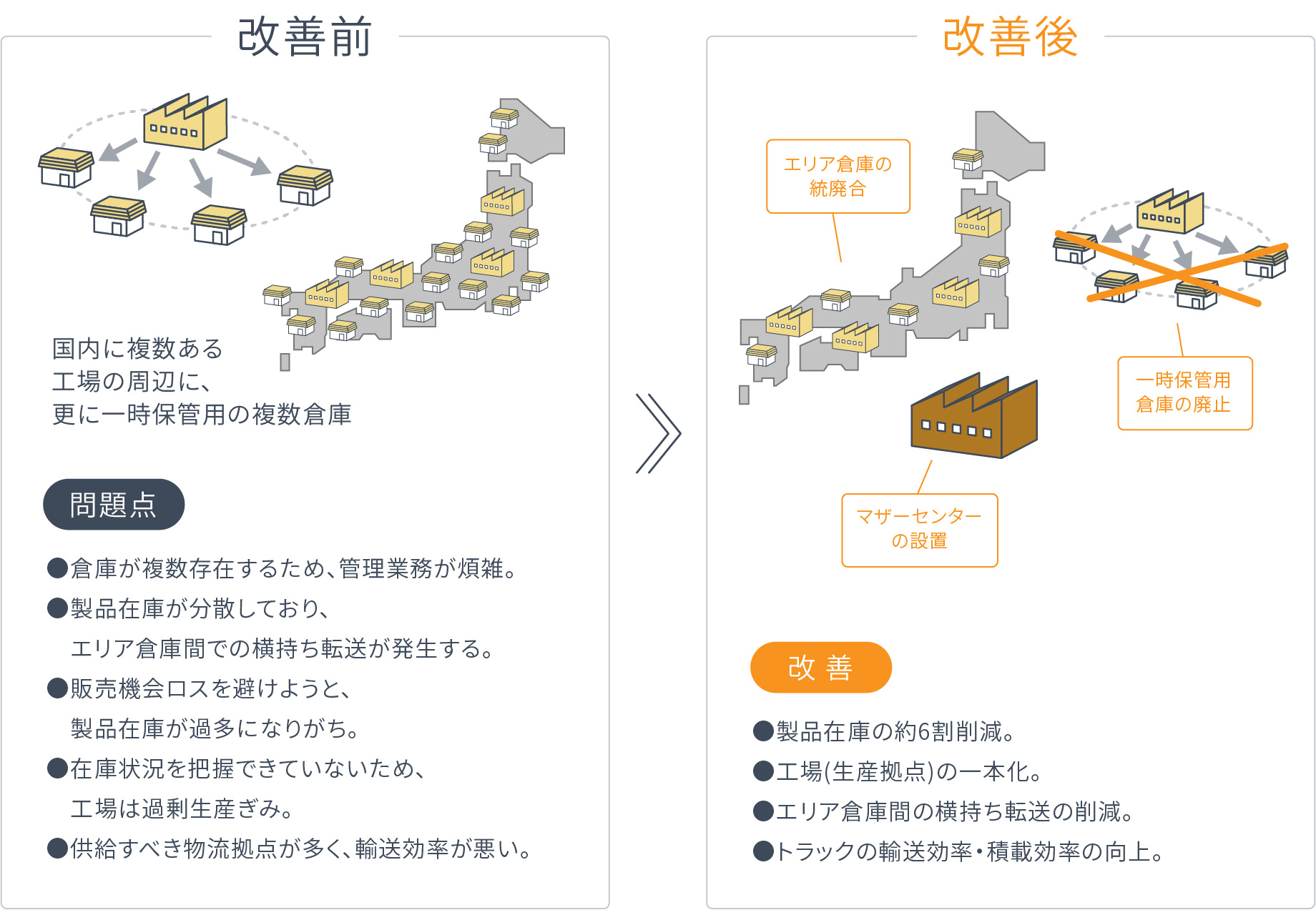
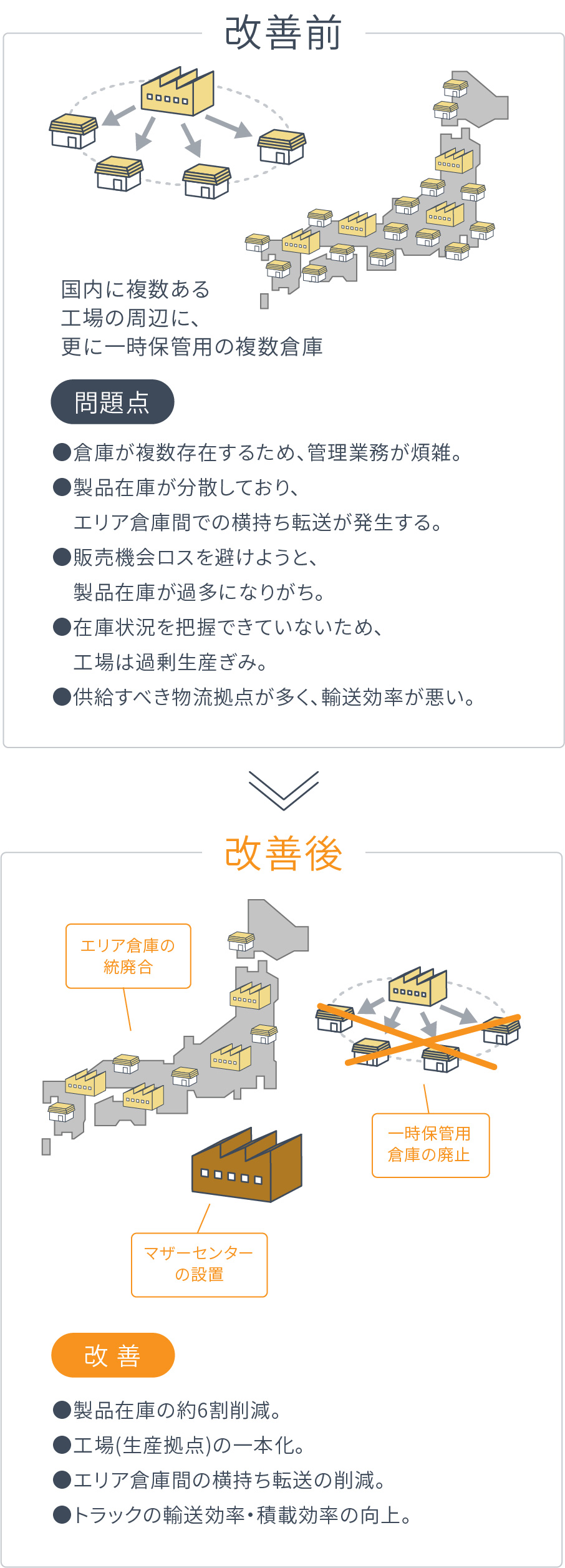
B社様は日本国内に複数の工場を運営しており、各工場周辺には製品を一時保管するための倉庫も設置していました。さらに、北海道から九州までの各エリアに倉庫を配置し、製品の在庫保管を行うという物流体制を構築していました。しかし、この体制にはいくつかの問題がありました。
1.倉庫が多数存在するため、管理業務が煩雑になり、効率的な運営が難しくなる。
2.製品在庫が分散しているため、エリア倉庫間での横持ち転送が発生し、物流コストが増加する。
3.販売機会のロスを避けるため、エリア倉庫の在庫が過剰になりがちで、無駄な在庫を抱えることになる。
4.各エリア倉庫の在庫状況を適切に把握できていないため、工場が過剰生産を行う必要が生じ、在庫の不均衡が生まれる。
5.供給すべき物流拠点が多いため、例えば工場からエリア倉庫への輸送効率が悪化し、輸送コストや時間が増大する。
これらの課題により、効率的な物流運営が難しくなっていました。
提案と成果
2年をかけて倉庫集約を実施し、物流コストの削減および物流業務の効率化を実現
1.工場に隣接するマザーセンターを設置し、既存の一時保管用倉庫を廃止。
2.エリア倉庫を全国9カ所から4カ所に削減。
3.エリア倉庫に製品在庫がない場合は、マザーセンターから顧客へ直接配送。
4.マザーセンターと需給部門との情報共有を強化し、在庫引き当てなどの業務を効率化。
これらの改革を約2年かけて実行しました。その結果、以下の成果を達成しました:
・製品在庫の約6割削減
・工場(生産拠点)の一本化
・エリア倉庫間の横持ち転送削減
・トラックの輸送効率および積載効率の向上